当前GMP车间器具清洗机近些年开始在国内无菌制剂车间普及应用,本篇文章简述管道工艺、粗糙度、焊接工艺的要求,供制药用户参考。
1、316L不锈钢材质的焊接应采用氩气保护焊,焊材的内外侧均需要充氩气进行焊接保护(不得低于99.99%,建议使用99.999%以上的氩气)。
2、焊接过程中需要严格控制焊接质量。管道切口完成后,必须用专用锉刀处理管口毛刺,并对管道焊口内外壁进行清洁处理(最好用无尘布蘸酒精进行擦拭),完成后进行对口工作;焊口偏差量不得超过标准要求:内外壁偏差不得超过管道壁厚的15%。
3、焊口点焊时的焊点应尽量小,并且不得出现连续的点焊现象,点焊应为尽量小的焊点,直径不能大于2.0mm。对于小于4in(10.16cm)的管道,建议临时焊点的数量不超过6个。
4、焊接质量的放行需要通过内窥镜检查,内窥镜检查的比例为自动焊口的抽检比例(不低于20%),手工焊口需要100%检查。
5、建议重力排水,坡度要求:短运转和支架运转2%,长运转和切换面板0.5~2%。
6、2D标准:指主管内壁到阀门密封点的长度应小于支管直径的2倍。
7、计算方法
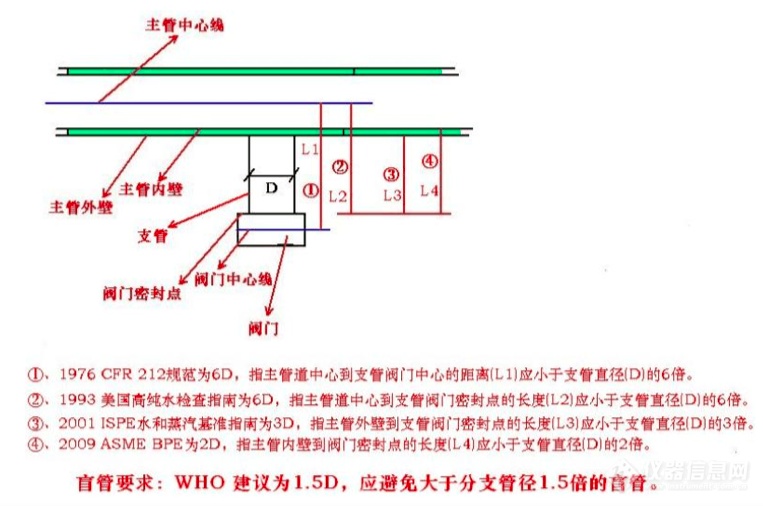
语瓶在应对以上要求中采取的措施:
1、 采用自动焊接技术+氩气保护;
2、 内窥镜报告齐全,自动焊接20%内窥镜检测,手工焊接100%内窥镜检测。
3、 清洗机管路设计标准:主要采用1.5D标准设计、部分采用2D标准设计
4、 内腔坡度≥3%,排水管路坡度≥0.5%;重力排水设计,确保管路排净
5、 腔内表面表面粗糙度Ra≤0.4μm,循环管路内表面粗糙度Ra≤0.6μm,循环管路外表面粗糙度Ra≤0.8μm。
6、通过计算流体力学(CFD)模拟介质流动特性,优化管道布局以减少湍流和压降,确保无死角设计(如支管长度≤2倍管径)
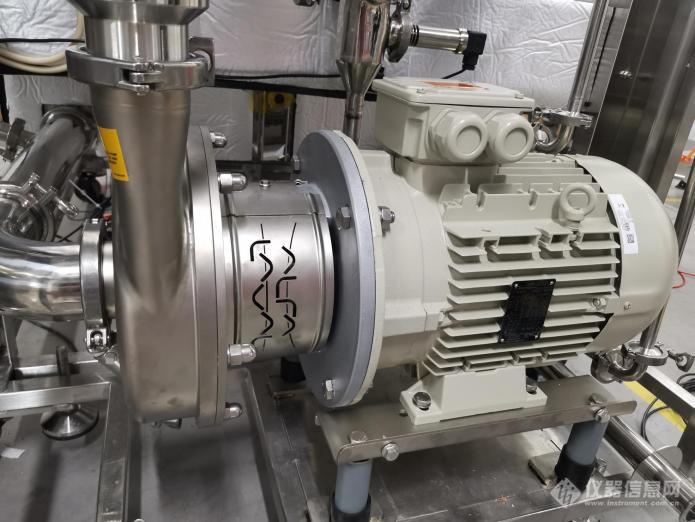
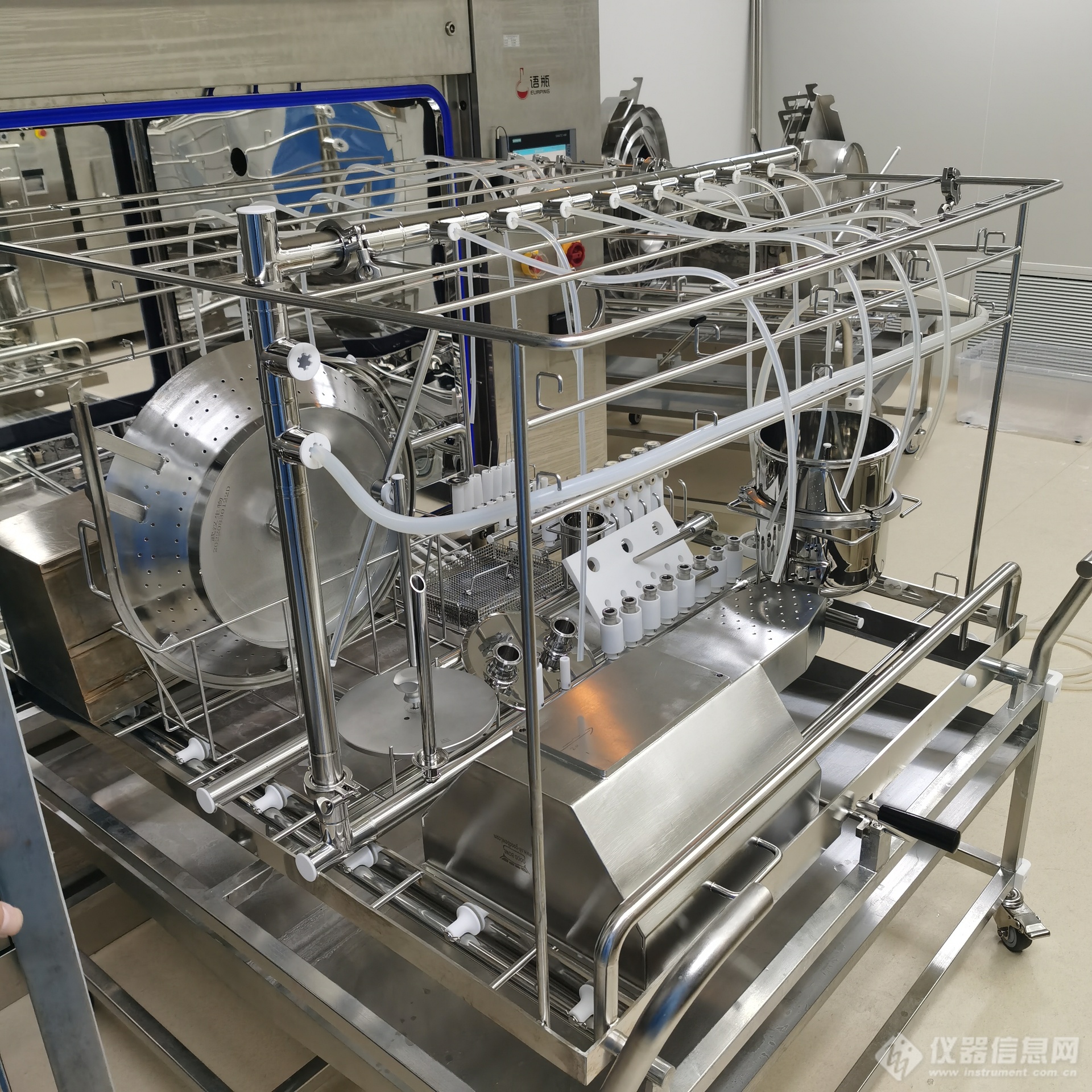
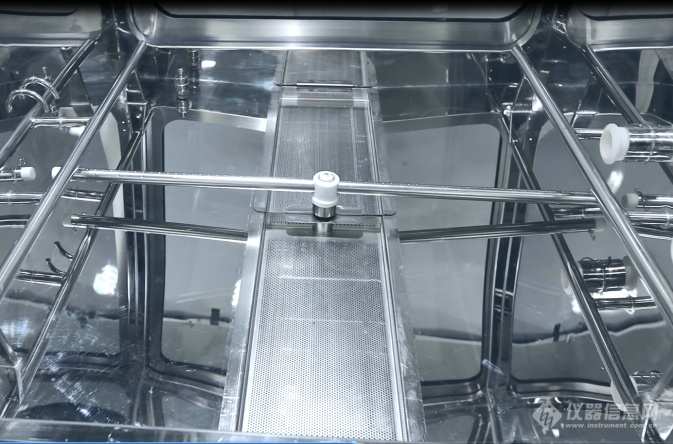
总结:
在清洗机设计中,工艺是至关重要的,用户在考察购买清洗机、以及是购买后的重要验证项目:
设计与清洁优化
1. 卫生设计原则
无死角结构:2D标准和坡度设计(坡度≥3%),确保流体完全排空,减少残留污染。例如,采用集成排净功能的阀门设计可避免液体积聚。
可清洁性验证:支持在位清洗(CIP)和蒸汽灭菌(SIP),通过核黄素覆盖率测试验证喷淋系统有效性,覆盖率需≥95%。
2. 流体动力学优化
湍流控制:循环系统设计需维持纯化水流速≥1.5m/s,抑制微生物滋生,同时通过CFD模拟减少局部阻力,降低压降。
密封与防污染:双O型圈或卡箍连接确保密封性(泄漏率≤1×10⁻⁶ mbar·L/s),避免交叉污染。
三、合规与成本效益
1. 法规符合性
全球认可度:ASME BPE被30多个国家采纳,符合FDA、WHO等机构的GMP要求,尤其适用于无菌制剂和生物制品的生产认证。例如,新版中国GMP(2010修订)明确推荐采用ASME BPE标准设计洁净管道。
验证支持:标准提供验证模板(如钝化层检测、残留铁测试),简化审计文件准备,缩短验证周期。
2. 全生命周期成本降低
维护便捷性:标准化卡箍接头和快装设计减少停机时间
耐久性提升:高耐腐蚀材料和表面处理延长设备寿命,例如316L不锈钢在高温蒸汽环境下仍能保持稳定性;
四、可持续性与市场竞争力
1. 环保兼容性
通过清洗机清洗减少化学试剂用量,并支持绿色工艺(如超滤膜技术)的集成,降低废水处理成本。
材料可追溯性(如炉号标识)支持循环经济,符合制药供应链倡议(PSCI)的可持续发展要求。
2. 技术壁垒构建
符合ASME BPE的设备可作为企业技术能力的证明,例如在疫苗生产、单克隆抗体工艺中凸显竞争优势。
通过数字化管理(如三维模型与MES系统对接),实现工艺参数的实时优化,提升生产效率。
采用ASME BPE标准不仅通过材料、设计和验证的严格规范保障了产品质量与合规性,还通过可清洁性优化和成本控制提升了生产效率和市场竞争力。其价值在生物制药等高要求领域中尤为显著,例如疫苗生产管道的无菌保障、注射用水系统的长期稳定性等场景。